Industrial DeNOx Systems - Services Market
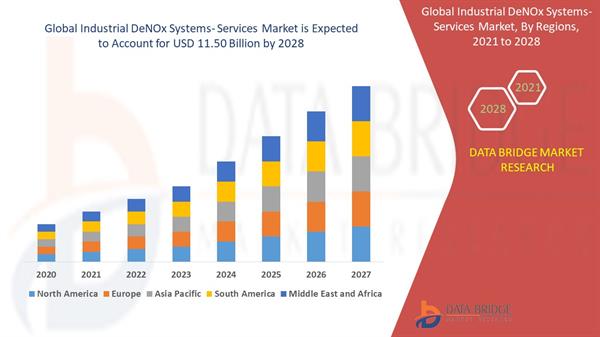
Selective Non-Catalytic Reduction (SNCR)
SNCR systems offer a more cost-effective alternative to SCR, especially for smaller industrial operations or facilities with limited budgets. Instead of relying on a catalyst, SNCR systems inject a reagent—typically urea or ammonia—directly into the combustion chamber or downstream at high temperatures (850–1100°C). The heat causes the NOx to react with the reagent, forming nitrogen and water.
While the NOx reduction efficiency of SNCR (typically 30–70%) is lower than SCR, it still meets many regulatory thresholds, particularly in regions where air quality standards are less stringent or during the early stages of compliance. The simplicity of the system—no catalysts, smaller footprint, lower capital and operational expenditure—makes SNCR particularly attractive for retrofitting existing plants.
However, one of the limitations of SNCR systems is the narrow temperature window required for effective reduction. Inject the reagent too early, and it decomposes without reacting. Too late, and NOx passes through untreated. This makes precise control systems and real-time monitoring essential for optimal performance—creating opportunities for service providers specializing in calibration, optimization, and performance audits.
In the coming years, we’ll see more hybrid approaches where SNCR serves as a pre-treatment stage before gases reach an SCR system, allowing industries to balance performance with cost-efficiency.
Hybrid Systems and Innovations
As industries continue to seek the perfect blend of efficiency and economy, hybrid DeNOx systems have emerged as a powerful solution. These systems combine the high efficiency of SCR with the cost-saving benefits of SNCR, delivering a more flexible and responsive emission control strategy.
Hybrid systems typically start with SNCR in the furnace zone to knock out the bulk of NOx emissions, followed by SCR downstream for polishing the remainder. This two-tiered approach significantly reduces ammonia consumption, catalyst volume, and overall system wear—without compromising on environmental compliance.
Beyond this, the DeNOx landscape is seeing a wave of innovation. Some of the most promising developments include:
-
Catalyst advancements: New materials like zeolites and mixed metal oxides are increasing SCR effectiveness at lower temperatures and extending catalyst lifespans.
-
Modular system designs: Pre-engineered modules reduce installation time and make upgrades easier, particularly in constrained facilities.
-
Digital control platforms: AI-driven systems now optimize reagent dosing and monitor flue gas parameters in real-time, improving efficiency and reducing human error.
These innovations are redefining what’s possible with DeNOx technologies, and service providers who stay on the cutting edge of these trends will gain a significant market advantage.
Components and Design of DeNOx Systems
Core Components of DeNOx Installations
Understanding the hardware that powers DeNOx systems is key to appreciating their complexity and performance demands. Whether it’s SCR or SNCR, all systems share some critical components that must be carefully engineered and maintained:
-
Reagent Storage and Dosing Units: This is where urea or ammonia is stored, often in bulk tanks, and then dosed precisely into the flue gas stream. These units require robust safety features due to the hazardous nature of the chemicals.
-
Injection Grids: For effective NOx reduction, reagents must be uniformly mixed with the flue gases. Injection grids are designed based on CFD simulations to ensure complete coverage and optimal reaction conditions.
-
Catalyst Modules (in SCR): These are the heart of SCR systems, typically made from vanadium, titanium, or zeolite-based materials, arranged in honeycomb or plate formats. Their performance degrades over time, requiring regular cleaning or replacement.
-
Control Systems: Modern DeNOx systems use PLC or DCS-based controllers for reagent flow, temperature monitoring, and feedback loops. These systems are essential for maximizing efficiency and minimizing reagent waste.
-
Heat Exchangers and Reactors: These manage flue gas temperatures and create optimal reaction conditions, especially in retrofitted systems where upstream heat recovery is part of the process.
Maintenance and service packages for these components have become a significant segment of the market, particularly with the rise of predictive maintenance technologies.
Engineering and Customization Considerations
No two industrial sites are alike, and DeNOx system designs must be tailored to suit specific operational conditions, fuel types, emission profiles, and regulatory requirements. This makes engineering and customization a vital part of any DeNOx project.
Custom designs must factor in:
-
Flue gas composition and flow rates
-
Operating temperatures and pressure drops
-
Available space for system integration
-
Compatibility with existing pollution control devices like ESPs or baghouses
For example, a coal-fired power plant in India might face space limitations and require a vertical reactor tower with an integrated SCR unit, while a biomass plant in Scandinavia might demand low-temperature SCR due to variable heat profiles.
Designing such bespoke solutions involves multi-disciplinary engineering—fluid dynamics, thermodynamics, materials science—and this has given rise to a new class of DeNOx service providers: engineering consultants, 3D simulation specialists, and turnkey EPC (engineering, procurement, construction) firms.
With global emissions standards tightening, there’s a growing market for high-performance, low-footprint systems that not only meet today’s requirements but are scalable for future upgrades—especially as carbon capture and green hydrogen integrations become mainstream.
Industrial Applications of DeNOx Systems
Power Generation Industry
The power sector remains the single largest application area for DeNOx systems, particularly coal-fired, gas-fired, and biomass power plants. These facilities operate at high temperatures and burn large volumes of fuel, making them prime sources of NOx emissions.
In developed countries, power plants must comply with stringent NOx limits—often under 100 mg/Nm³—pushing operators toward advanced SCR systems integrated with real-time monitoring. In contrast, developing nations are now catching up, with India, China, and Southeast Asia rolling out mandates for ultra-low NOx emissions across both public and private generation sectors.
Beyond compliance, DeNOx systems help power plants improve combustion efficiency and reduce fouling in boilers and turbines. This leads to lower operational costs and increased equipment lifespan, offsetting some of the initial capital investment.
Services in this segment range from system design and retrofits to catalyst management, reagent supply logistics, and performance optimization. There’s also a growing demand for mobile DeNOx units for temporary power plants and emergency generators—highlighting how versatile and vital these systems have become in today’s energy mix.
https://www.databridgemarketresearch.com/reports/global-party-balloon-market
https://www.databridgemarketresearch.com/reports/global-multimodal-imaging-market
https://www.databridgemarketresearch.com/reports/global-povidone-iodine-market
https://www.databridgemarketresearch.com/reports/global-boxing-equipment-market
https://www.databridgemarketresearch.com/reports/global-aortic-repair-devices-market